SimuWarp, our add-on for Abaqus, enables Abaqus to be used for advanced composite warpage simulation. Use your existing software architecture to predict process-induced distortions of composite structures!


Our Abaqus/CAE plugin offers automated model setup for warpage simulations. This facilitates and speeds-up your simulation workflow, and ensures that all relevant aspects of the model are setup correctly.

Accurate material modeling is key for sophisticated composite warpage simulation. SimuWarp includes extensive material models and thereby allows to consider all material characteristics, which are vital for reliable warpage prediction with thermoplastic and thermosetting materials.

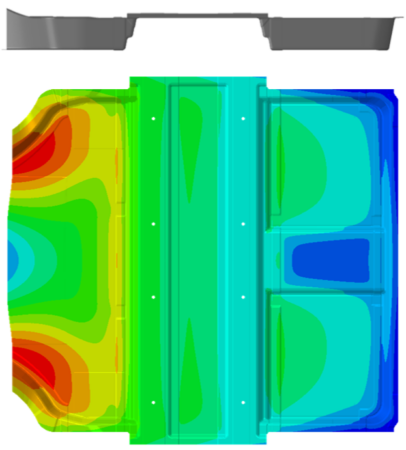
Warpage analysis of a composite car floor structure manufactured using resin transfer molding (RTM)
Key features
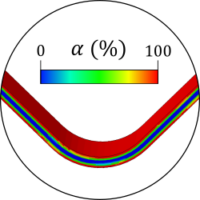
Thermokinetic simulation
A precise analysis of the heating and cooling processes is vital for predicting process-induced residual strains. Our simulation tools accurately model the temperature distribution and contain sophisticated models to derive shrinkage strains due to cross-linking or crystallization. This analysis can be done either as part of a fully featured warpage simulation or standalone, e.g., for a quick assessment of a cooling system design.
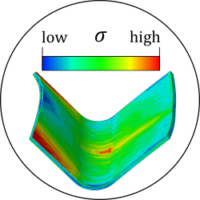
Structural performance assessment
Predicting process-induced residual stresses enables a better estimation of the expected performance of the part. Important aspects are, for instance, fatigue or strength. Transferring the warpage simulation results to other numerical models can be achieved using SimuChain.
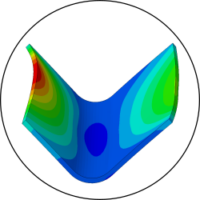
Warpage prediction of components
Warpage is caused by shrinkage strains due to changes in temperature or morphology of the polymer. Depending on the applied thermal boundary conditions, stress gradients in the through-thickness direction lead to a deformation of the part’s shape. When using composite materials, the distribution and orientation of fibers are additional sources of stress gradients. Calculating the resulting stress state enables to predict the corresponding part deformation and to check whether prescribed tolerances will be met.
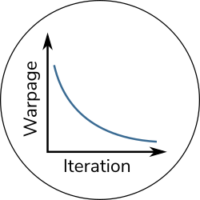
Warpage optimization
A warpage simulation incorporates many aspects defined during part and process design. It can therefore be utilized to determine the sensitivity of the resulting part shape with respect to these design variables. Among others, this allows minimization of warpage or a deliberate adjustment of the part’s shape. The latter might be used to provoke a specific residual stress state which is beneficial for the targeted application of the part.
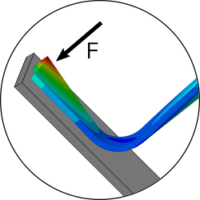
Warpage prediction of assemblies
If a warped component is part of a larger assembly, deformation of the individual component and connected parts will occur after mounting. This deformation can be predicted by incorporating the assembly into the simulation model without the need to conduct expensive experimental trials.
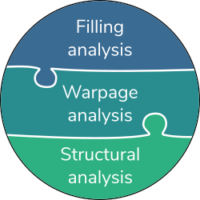
Continuous integration in CAE chains
SimuWarp can be integrated with existing CAE tool chains to import initial conditions like fiber orientation or temperature from preceding simulations. Similarly, the results of SimuWarp can be exported for use in downstream numerical analyses. This result transfer (mapping) is supported by SimuWarp.
Materials & Technologies
SimuWarp supports materials and processes relevant to large-scale production. This includes continuously and discontinuously reinforced composites based on thermosetting and thermoplastic matrix systems. Moreover, hybrid material designs, e.g. a combination of LFT and unidirectional tapes, are also supported.
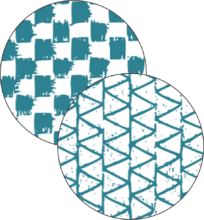
Continuously fiber-reinforced composites
Continuously fiber-reinforced composites are modeled in SimuWarp in form of laminates which usually consist of several differently oriented plies. The local fiber orientation of these individual plies is the result of a forming process step and an important quantity for accurate prediction of warpage. Forming of such a stack of textiles therefore needs to be predicted beforehand e.g. by using SimuDrape.
Supported manufacturing processes:
- Compression molding of thermoplastic tape laminates, Organosheets or thermoset prepregs
- Resin transfer molding processes based on dry engineering textiles like non-crimp fabrics (UD-NCF) or woven fabrics
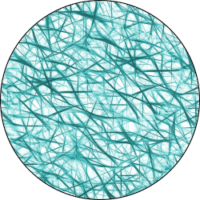
Discontinuously fiber-reinforced composites
Parts made of discontinuously fiber-reinforced composites are shaped during a molding process. As this involves a significant flow of the filled polymer material, important properties like fiber orientation or temperature are constantly altered during mold filling. The resulting spatial distribution of such properties are vital input parameters for a meaningful warpage simulation. The SimuWarp add-on for Moldflow allows the calculation of the required data beforehand and the SimuWarp add-on for Abaqus can be used to transfer the data to the warpage simulation model.?
Supported manufacturing processes:
- Compression molding of long-fiber-reinforced thermoplastics (LFT), glass mat thermoplastics (GMT), and sheet molding compound (SMC)
- Injection molding with or without fibers
Any questions?
Interested in a trial license?
Do not hesitate to get in contact with us. We are pleased if you leave us a message!