SimuDrape, our add-on for Abaqus, enables Abaqus to be used for advanced composite forming simulation. Use your existing software architecture for advanced forming simulations!


A fully automatized model setup for stamp and membrane forming processes is enabled through the SimuDrape ABAQUS/CAE plugin. Based on this, models are created without modeling errors in a time-efficient manner.

Advanced material modeling is key for accurate composite forming simulation. SimuDrape provides material models accounting for the specificities in composite forming simulation with engineering textiles, thermoplastic tape laminates, and prepreg materials in Abaqus/Explicit.

Short video: Local fiber orientation prediction with SimuDrape.
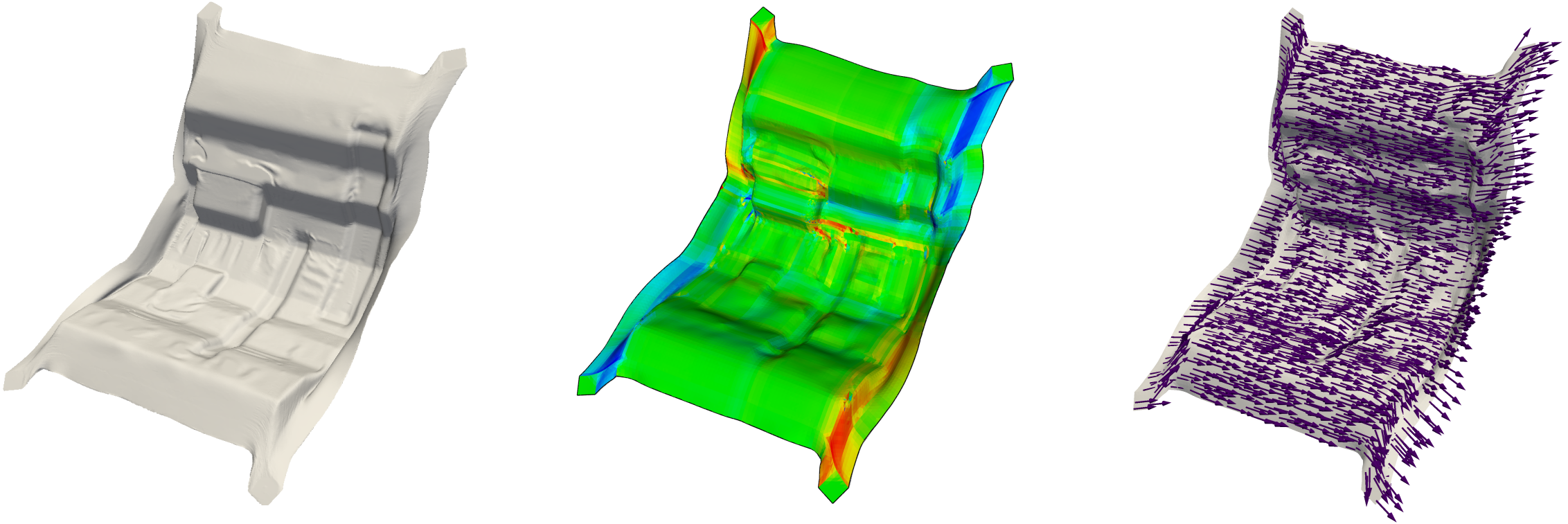
Visualization of an exemplary forming simulation result:
Left: Surface scan of the physical part, middle: Shear strain prediction, right: Local fiber orientation prediction.
Key features
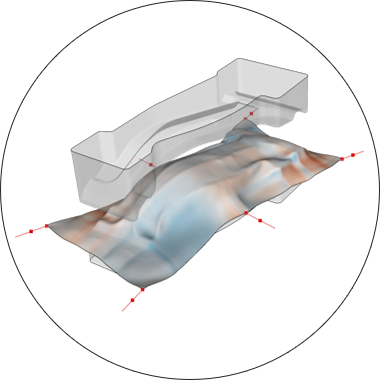
Gripper modeling
Grippers are valuable utility to enable defect-free forming. SimuDrape provides accurate gripper modeling approaches taking into account kinematics and load application and, thus, enables the optimization of gripper setups.
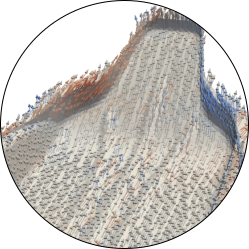
Fiber orientation prediction
Forming induces a local change in fiber orientation. The local fiber orientation can be predicted by SimuDrape and transferred to downstream FEA by SimuChain, our Abaqus add-on for setting up a virtual process chain, to increase the prediction accuracy of FEA.
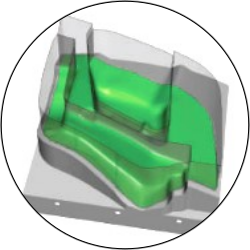
Tailoring determination
Near-net-shaped forming enables the reduction of material waste and thus increases material efficiency. SimuDrape enables the determination of the results from composite forming simulation to determine a suitable tailoring for near-net-shaped forming.
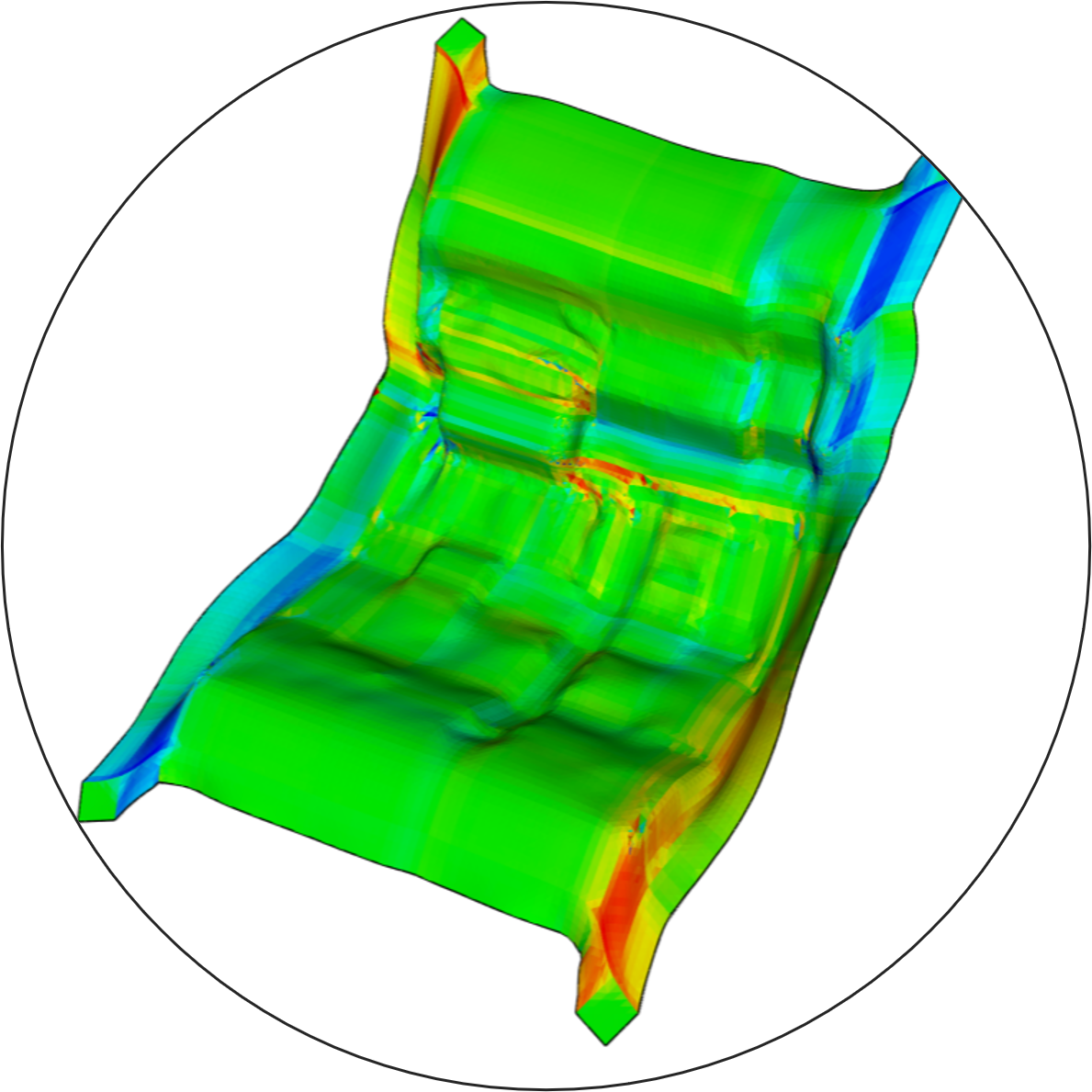
Defect prediction
Composites forming might go along with defects, such as local wrinkling or gapping. Composites forming simulation is capable to predict local defects and thus can be used to validate and optimize the manufacturability of a specific geometry.
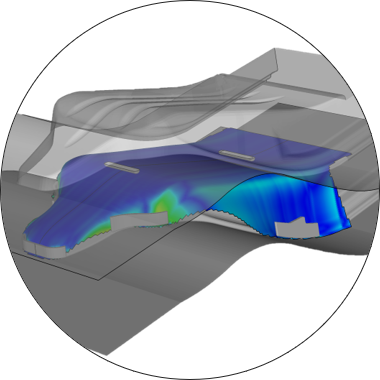
Sequential draping
Sequential forming concepts can facilitate the forming process by mimicking a hand-draping process. SimuDrape allows the automatic model setup with an arbitrary number of stamps and therefore virtual optimization of arbitrary sequential draping concepts.
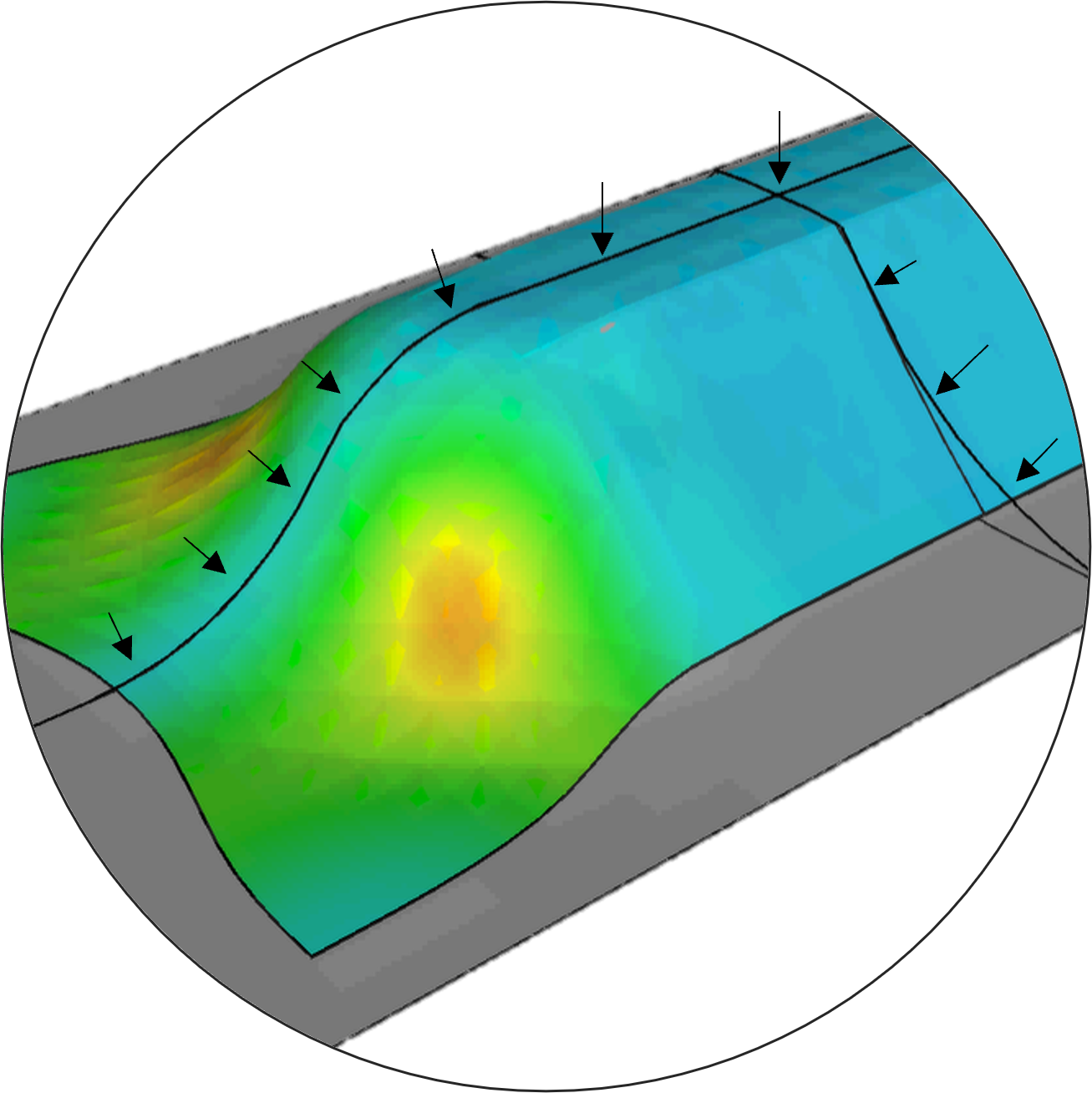
Membrane forming
The use of vacuum-assisted processes with a deformable membrane enables forming of large components. SimuDrape supports the automatic model setup for membrane forming processes and membrane modeling using hyperelastic material modeling.
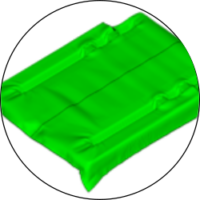
Initial charge forming
Compression molding of SMC, GMT, or LFT might go along with material forming before the onset of material flow. SimuDrape enables modeling material forming in Abaqus these chopped fiber materials. The result is the formed geometry at the onset of material flow including the local fiber orientation predicted by well-known models (Jefferey, Folgar-Tucker, ARD-RSC).
Materials & Technologies
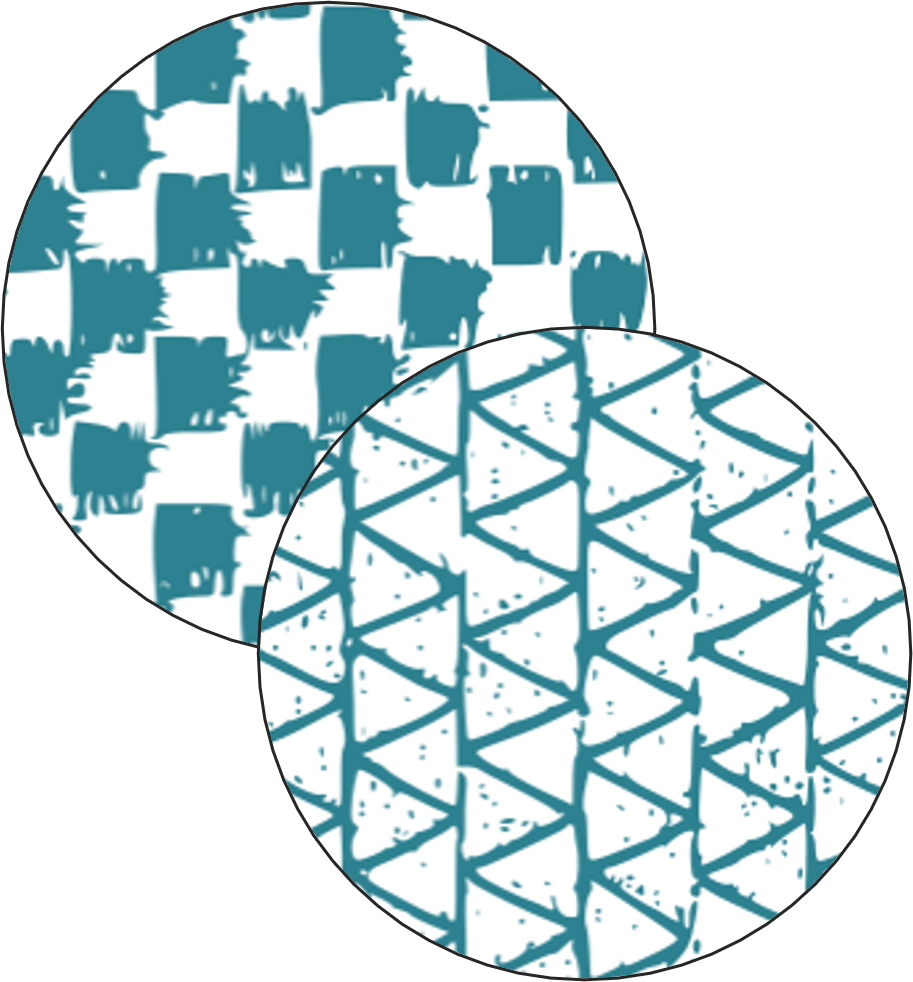
Non-crimp fabrics (NCF) & woven fabrics
Forming engineering textiles is an essential process step before infiltration with a resin, e.g. as part of the Resin Transfer Molding (RTM) technology.
The currently deployed version of SimuDrape supports the modeling of woven fabrics.
We currently work on making a modeling approach for unidirectional, biaxial, and triaxial non-crimp fabrics (NCFs) available. Stay tuned for updates!
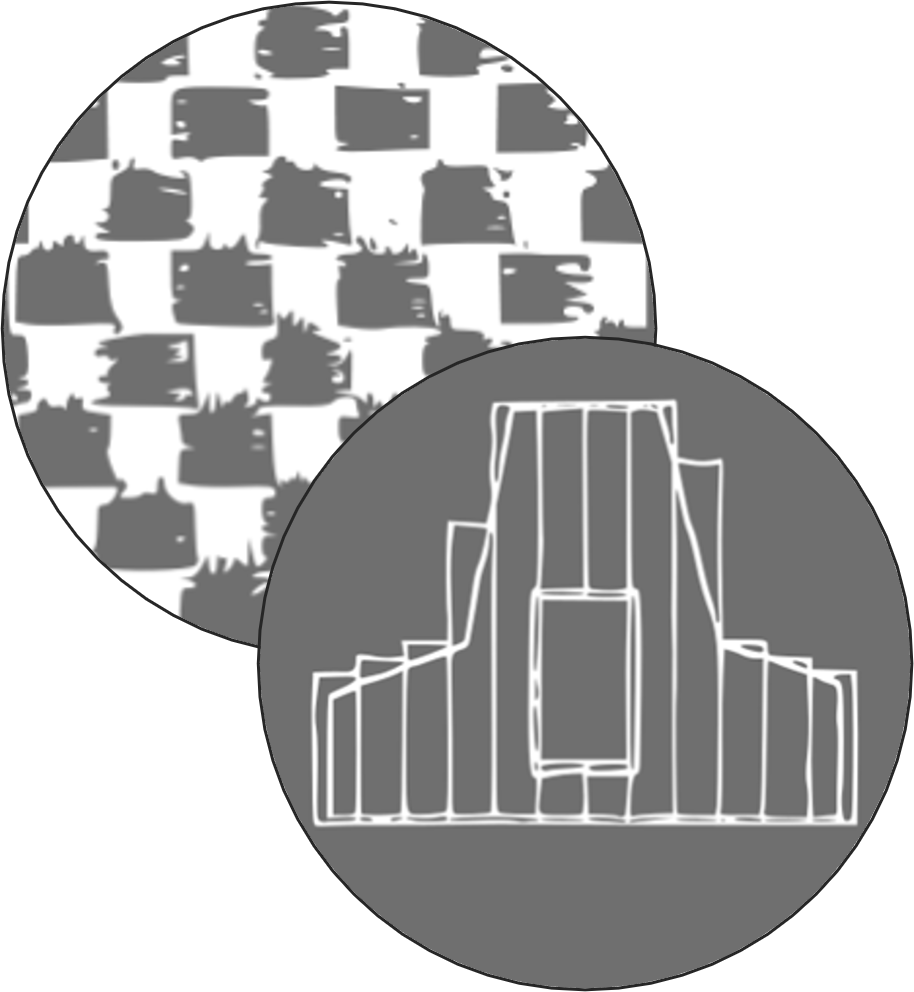
Thermoplastic tape laminates, organosheets & thermoset prepregs
Continuous reinforcements with a thermoplastic matrix are broadly applied in industrial applications. In addition, thermoset prepregs play a major role.
The currently deployed version of SimuDrape supports modeling thermoplastic tape laminates, organosheets, and thermoset prepregs. For thermoplastic materials, we support both an isothermal analysis as well as a thermokinetical-thermomechanical analysis.
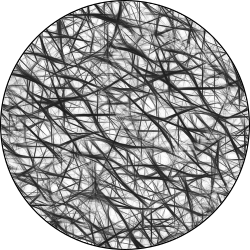
DISCONTINUOUSLY FIBER-REINFORCED COMPOSITES
Chopped fiber materials are processed using compression molding technologies through material flow. Compression molding of GMT, LFT, and SMC, however, can involve material forming prior to material flow. SimuDrape provides material models to accurately describe chopped fiber-reinforced composites during forming. Based on this, a sequential molding simulation approach can be established, which covers the stages of material forming (SimuDrape) and material flow (e.g. Moldflow).
Related Case Studies
Macroscopic Draping Simulation for Non-Crimp Fabrics (NCF)
Modeling draping on the macroscopic level is essential for efficiently simulating industrial-scale components. Most simulations of NCF have been conducted at the mesoscopic level, where the fibers and the stitching are captured discretely. More recently, NCF models have also been developed at the macroscopic level by KIT-FAST and made available through SimuDrape. This macroscopic approach for NCF draping simulation has been adopted in the public-funded project ELECTRA and applied to a complexly shaped aerospace structure.
3D Skeleton Winding (3DSW) Lightweight Structures
The 3D skeleton winding (3DSW) technology uses injection overmolded fiber skeletons. The amount of continuous fibers is reduced drastically by using load path-appropriate fiber skeletons. In combination with an optimized overmolding structure cost-efficient lightweight structures are achieved. A CE-certified winding cell as well as a virtual optimization and validation approach for 3DSW structures have been developed in the Korean German ZIM project ACCORD.
Molding Simulation for Glass Mat Thermoplastics (GMT)
In this case study, a molding simulation for GMT materials is presented. The considered material is TEPEX® flowcore 102-RGR2400/47%, a GMT with an engineering polymer, i.e. PA6, which is manufactured by Lanxess, Bond Laminates.
The results originate from a collaboration project between General Motors Research & Development, the University of Western Ontario (UWO), and the Institute for Vehicle System Technology (FAST) of the Karlsruhe Institute of Technology (KIT) and have been published previously by Dörr.
Any questions?
Interested in a trial license?
Do not hesitate to get in contact with us. We are pleased if you leave us a message!