SimuFill, our add-on for Moldflow, enables advanced compression and injection molding analyses. Improve your existing software architecture for modeling molding processes!


The Moldflow add-on provided through SimuFill enables modeling the pvT behavior as a function of the degree of conversion. This includes predicting the crystallization kinetics and curing kinetics for thermoplastics and thermosets, respectively.

Short video: Virtual process chain for SMC.
Key features
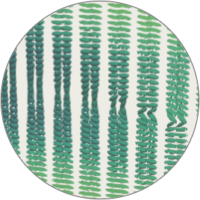
D-LFT fiber orientation
D-LFT strands are manufactured in an extrusion process, which induces a local fiber orientation. Use our approaches to initialize the local fiber orientation in D-LFT strands, as the basis for accurate prediction of the fiber orientation in the final part.
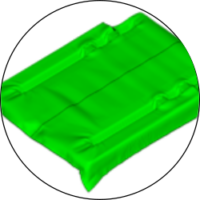
Data transfer
SimuFill enables the data transfer between Abaqus and Moldflow. This enables modeling material forming and material flow in Abaqus and Moldflow, respectively. Based on this, the best-suited numerical technique is used for each stage.
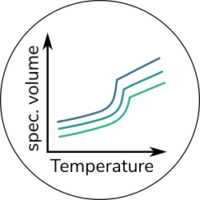
pvT modeling
Accurate modeling of the pvT behavior is crucial for the accurate prediction of residual strains due to thermal elongation and shrinkage. Residual strains in turn induce residual stresses and warpage. SimuFill provides sophisticated models for predicting the pvT behavior as a function of the degree of conversion for both, thermoplastics and thermosets.
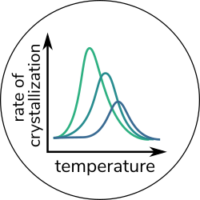
Crystallization kinetics
Accurate prediction of crystallization kinetics ensures accurate prediction of mold filling and part warpage/spring-in. SimuFill provides the Nakamura-Ziabicki model for Moldflow, which is also used by SimuWarp, our add-on for warpage analyses in Abaqus.
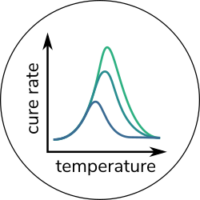
Curing kinetics
Accurate prediction of curing kinetics ensures accurate prediction of mold filling and part warpage/spring-in. SimuFill provides different curing kinetics models for Moldflow, which are used by SimuWarp, our add-on for warpage analyses in Abaqus.
Materials & Technologies
We support materials and processing technologies relevant to large-scale production, ranging from sheet molding compound (SMC), over long-fiber-reinforced thermoplastics (LFT), to glass mat thermoplastics (GMT). This includes the combination of chopped fiber materials with tapes or prepregs through local reinforcements or sandwich structures.
Thermoplastic compression molding
Reactive compression molding
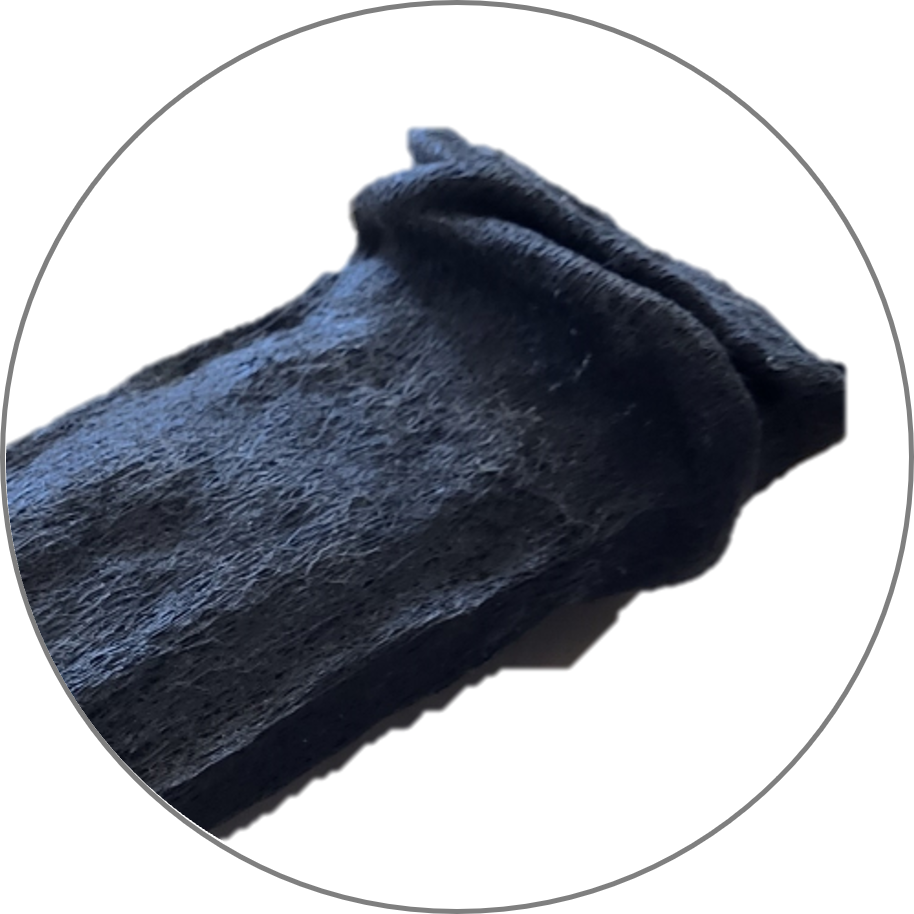
Long-fiber-reinforced thermoplastics (LFT)
Compression molding of LFT or tape LFT sandwiches are widespread processes to produce large-scale parts with high geometric complexity.
SimuFill enables the initialization of fiber orientation in LFT strands. Moreover, modeling crystallization kinetics as well as the pvT behavior as a function of the degree of conversion as the basis for accurate warpage predictions is enabled.
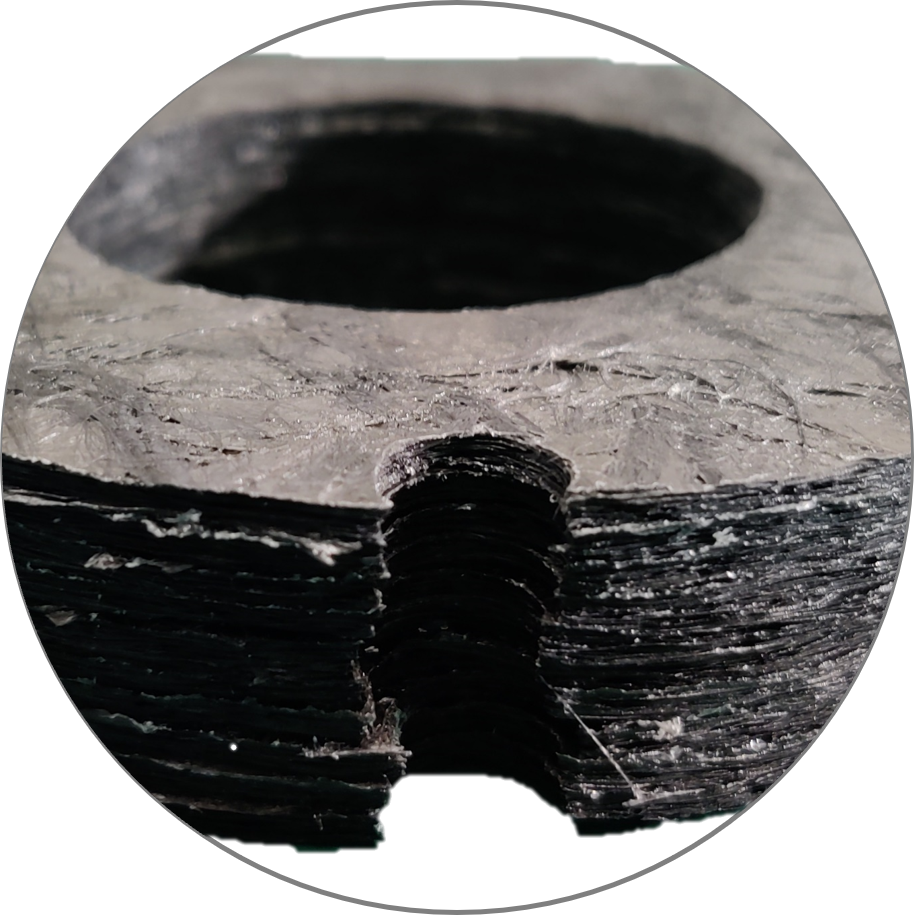
Sheet molding compound (SMC)
Compression molding of SMC is an established process to produce large-scale parts with a high geometric complexity for applications at elevated temperatures.?
SimuFill enables the transfer of forming simulation results from SimuDrape to Moldlfow, including the local fiber orientation. Based on this, the best-suited numerical technique is used for each stage, namely material forming and material flow.?
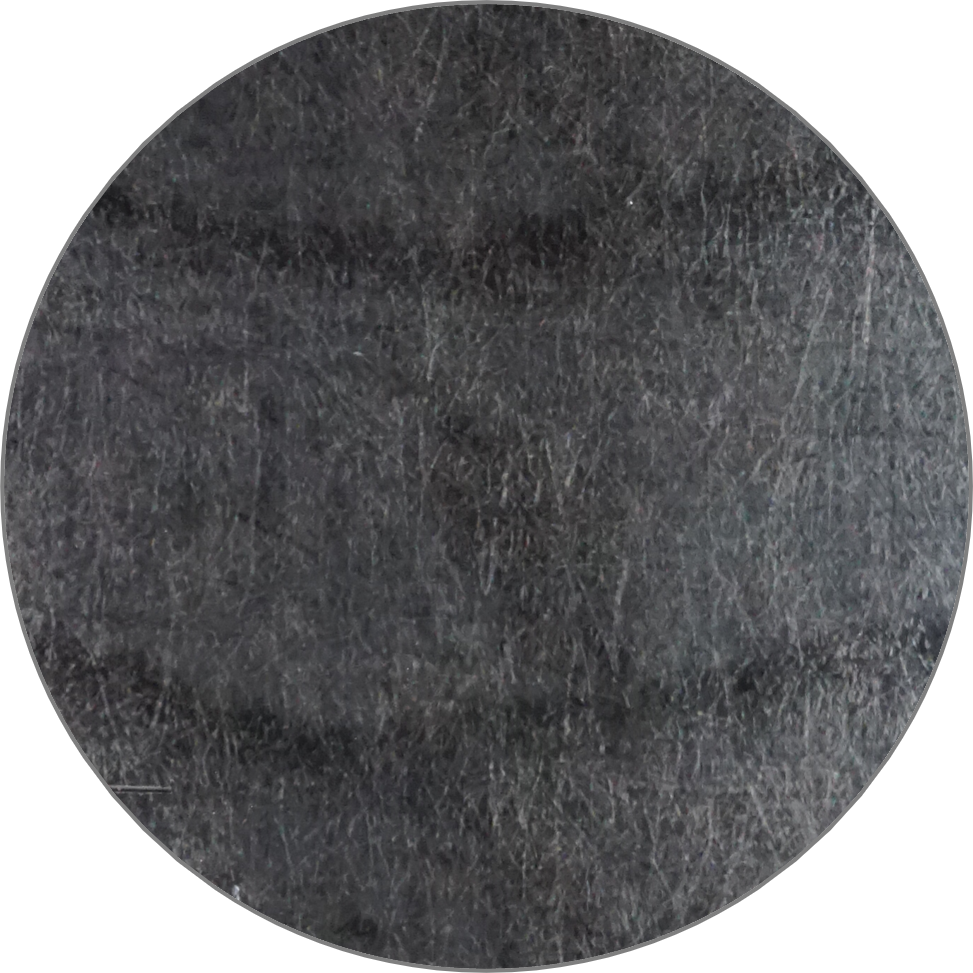
Glass mat thermoplastics (GMT)
Compression molding of GMT is an established process to produce low-cost parts with a low degree of geometric complexity and higher demand in mechanical properties compared to LFT.?
SimuFill enables the transfer of forming simulation results from SimuDrape to Moldlfow, including the local fiber orientation. Based on this, the best-suited numerical technique is used for each stage, namely material forming and material flow.
Thermoplastic injection molding
Reactive injection molding
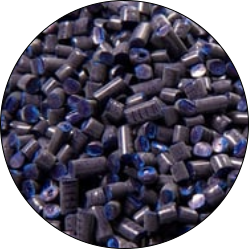
Thermoplastics and long-fiber-reinforced thermoplastics (LFT)
Injection molding with thermoplastics and long-fiber-reinforced thermoplastics (LFT) is a widely spread technology for high volumes and high geometric complexity.
SimuFill enables modeling crystallization kinetics as well as the pvT behavior as a function of the degree of conversion as the basis for accurate warpage predictions is enabled.
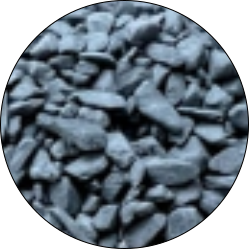
Thermoset injection molding
Reactive injection molding is a process technology for complex geometries with a higher demand for thermal resistance.
SimuFill enables modeling curing kinetics as well as the pvT behavior as a function of the degree of conversion as the basis for accurate warpage predictions is enabled.
Related Case Studies
Virtual Process Chain for LFT-Tape-Sandwiches
Underbody structures in battery electric vehicles (BEV) protect batteries against damage from below. Impact events, in particular, represent special challenges, as a significant energy amount must be absorbed within minimal deformation tolerances.
Within protECOlight, a significantly ribbed geometry was then investigated in a large process campaign to better understand the mechanisms of rib filling on top of the LFT-tape-sandwich and through the tape.
Virtual Process Chain for SMC Materials
In a collaboration project with Blackwave, the Simutence virtual process chain for SMC materials has been validated for the rim of a lightweight airplane.
Simutence uses an in-mold characterization approach to accurately characterize both the viscosity and the wall slip of the SMC. The acquired data is used to parameterize flow models built into commercial molding simulation software, such as Moldflow.
Benchmark of SMC molding Simulation Tools
There are a variety of different approaches for SMC molding simulation. In a collaboration project with Volkswagen (VW) and the Karlsruhe Institute of Technology (KIT), different molding simulation tools have been benchmarked for a honeycomb structure. Therefore, the prediction accuracy for the press force and the filling pattern was validated against experimental tests.
Molding Simulation for Glass Mat Thermoplastics (GMT)
In this case study, a molding simulation for GMT materials is presented. The considered material is TEPEX® flowcore 102-RGR2400/47%, a GMT with an engineering polymer, i.e. PA6, which is manufactured by Lanxess, Bond Laminates.
The results originate from a collaboration project between General Motors Research & Development, the University of Western Ontario (UWO), and the Institute for Vehicle System Technology (FAST) of the Karlsruhe Institute of Technology (KIT) and have been published previously by Dörr.
Advanced Virtual Process Design for Overmolding Processes
A sequential approach consisting of thermomechanical thermoforming simulation using SimuDrape and subsequent overmolding simulation in Moldflow was developed. This enables us to predict the temperature field during thermoforming and to consider it during overmolding simulation. A sensitivity study reveals that the temperature in the blank is sensitive to the temperature achieved in the overmolding interface and thus is critical for the interface strength.
Publications
- Rothenhäuser et al.: “Experimental and Numerical Analysis of SMC Compression Molding in Confined Regions—A Comparison of Simulation Approaches”, Journal of Composites Science, 2022.
- Görthofer et al.: “Virtual process chain of sheet molding compound: Development, validation and perspectives”, Composites Part B, 2019.
- Hohberg et al.: “Rheological Measurements and Rheological Shell Model considering the Compressible Behavior of Long Fiber Reinforced Sheet Molding Compound (SMC)”, Composites Part A, 2017.
Any questions?
Interested in a trial license?
Do not hesitate to get in contact with us. We are pleased if you leave us a message!