Structural simulation is a powerful digital instrument for predicting the mechanical performance of composite structures. The results provide insights into stiffness and strength, allowing for informed design decisions during product development, which can save time, costs, and resources.


The mechanical performance is determined through the local fiber structure, which in turn is significantly influenced by the manufacturing process. Neglecting manufacturing effects in structural analyses can yield inaccurate FEA results and thus both unexploited lightweight potential or apparent safety margins.

SimuChain, our add-on for Abaqus, creates a virtual process chain and enables us to consider manufacturing effects in structural simulation. We support structural analyses for chopped fiber materials (SMC, LFT, GMT) and continuously fiber-reinforced composites including nonlinear material modeling under quasi-static loading conditions.

Page Content
Short video: Virtual process chain for SMC.
Key features
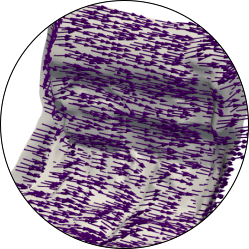
Local fiber orientation
Composite forming induces a change in the local fiber orientation. Composite forming simulation using e.g. SimuDrape enables the prediction of local fiber orientation. SimuChain supports the transfer of local fiber orientation predicted by composite forming simulation into FEA using laminate theories. Based on this, the local anisotropy of thermal and mechanical properties can be predicted for continuously fiber-reinforced composites.
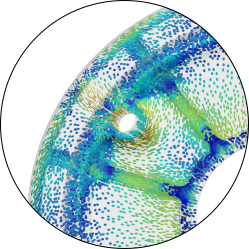
Homogenization
Molding of chopped fiber materials induces a change in the local fiber orientation. Molding simulation using e.g. SimuFill enables the prediction of the flow-induced local fiber orientation. SimuChain supports the homogenization of effective material properties using the properties of the fiber, matrix, and composite, as well as the local fiber orientation. Based on this, the local anisotropy of thermal and mechanical properties can be predicted for chopped fiber materials.
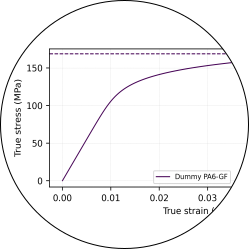
Nonlinear material modeling
The virtual design of composite structures often requires nonlinear material modeling, including for example viscoelasticity, plasticity, or damage. We support you with nonlinear material modeling in quasi-static loading conditions including the therefore-required materials characterization.
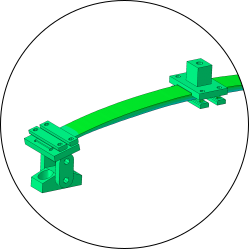
Components and assemblies
Structural analyses enable the virtual design of components and assemblies. We support both modeling components with suitable boundary conditions as well as modeling complex assemblies including contact conditions and constraints. In any case, we will support you in finding a modeling approach with the minimum possible but required complexity to enable time- and cost-efficient but accurate analyses.
Related Case Study
3D Skeleton Winding (3DSW) Lightweight Structures
The 3D skeleton winding (3DSW) technology uses injection overmolded fiber skeletons. The amount of continuous fibers is reduced drastically by using load path-appropriate fiber skeletons. In combination with an optimized overmolding structure cost-efficient lightweight structures are achieved. A CE-certified winding cell as well as a virtual optimization and validation approach for 3DSW structures have been developed in the Korean German ZIM project ACCORD.
Any questions?
Do not hesitate to get in contact with us. We are pleased if you leave us a message!